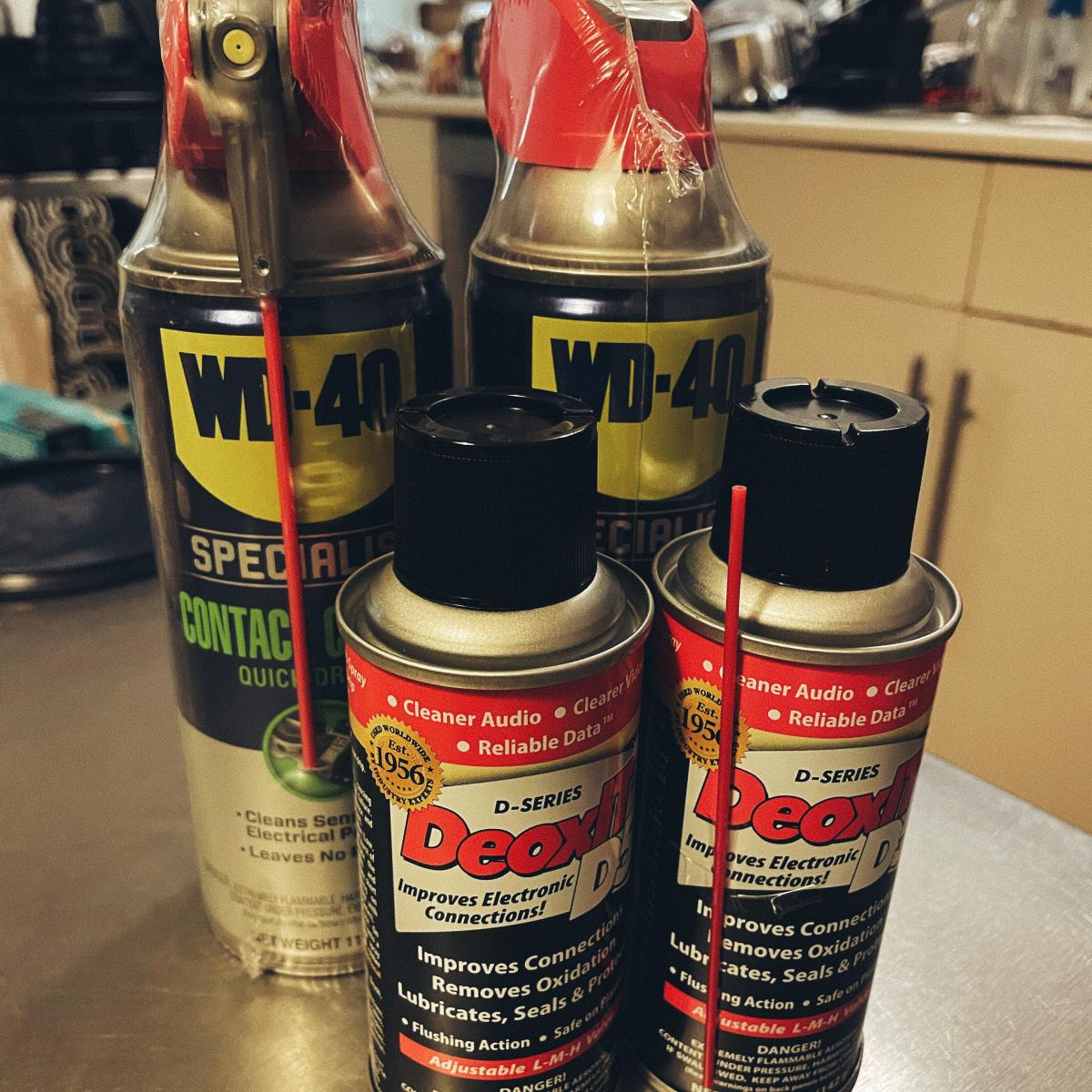
Some parts get lubricant, and some parts don’t. Don’t go wild with the DeoxIT, folks!
Service Checklist
Amp techs often throw around the phrase “service the amp,” but what does that really mean? Are all service technicians on the same page when they say they are going to give your amp “a full service?” Probably not. I know what’s on my page, though, and it seems like I’m always refining it, so I thought it would be helpful if I shared my checklist. Yes, it is an actual checklist. It can be hard to keep track of where you are on every repair when you have multiple items, waiting on parts, approvals, or for you to be finished with the previous thing.
Preflight
As always, before touching an open amplifier chassis on my bench, I unplug it from mains voltage and check all of the high voltage electrolytic capacitors for DC voltage. If necessary, I drain them accordingly and recheck them for voltage before proceeding.
Pots (and Rotary Switches)
Scratchy pots are a common issue on amplifiers. Even if they aren’t an issue, you still need to clean and lubricate every pot that crosses your bench because you don’t know if or when the amp will ever be serviced again! This isn’t the only issue to plague pots, though. They often require secure connections to ground, and spills, corrosion, and loose nuts can cause these to be unreliable. Here is my pots checklist and the steps I follow to ensure each potentiometer reaches it’s full potential:
- ☑️ Remove knobs
- ☑️ Clean faceplate and surrounding chassis
- ☑️ Clean and lubricate pots
- ☑️ Tighten nuts
- ☑️ Inspect solder joints and reflow if necessary
- ☑️ Clean knobs
- ☑️ Adjust knob spacing
- Remove the first knob
- Clean the faceplate under the knob
- Clean and lubricate the pot with the tiniest squirt of cleaner and lubricant (I use DeoxIT D5)
- If the nut or area around the pot looks corroded or dirty, disconnect and clean the area and components with alcohol.
- Tighten the nut back down securely.
- Clean the knob with dry or slightly damp toothbrush.
- Reinstall the knob with the end of a large zip tie behind it to measure spacing. This prevents rubbing and wear on the faceplate.
- Repeat for all the remaining pots.
Yes, I complete this entire process one pot at a time. It is a common misconception that batching tasks speeds things up. In fact, batching increases the chance for repeating mistakes and is actually slower! This method also makes it easier for me to keep track which pot I am on.
Jacks
Like pots, jacks also often provide critical connections to ground. In the case of effects loops, they can also lie directly in the signal path! Dirty or corroded shuts on an effects loop jack is a common cause of lost signal in a guitar amp. This is my jack checklist and the steps I follow to keep your jacks jacked up and good to go:
- ☑️ Remove jacks
- ☑️ Clean faceplate and surrounding chassis
- ☑️ Tighten nuts
- ☑️ Clean shunts
- ☑️ Clean tips
- ☑️ Clean sleeves
- ☑️ Tension shunts
- Inspect the nut, washer and area around the first jack. If anything looks corroded or dirty, disconnect and clean the area and components with alcohol.
- Tighten the nut back down securely.
- For phone jacks, clean the shutting connection by placing a phone plug partially in the jack and spraying a thin piece of cardboard liberally with non-lubricating contact cleaner, then inserting it between the tip and shunt, pulling the plug, and scrubbing it back and forth. Spray the same contact cleaner on a small bottle brush, and scrub in and out of the jack. This will also clean the tip connection.
- For RCA jacks, spray a smaller bottle brush with non-lubricating contact cleaner, and scrub in and out of the center of the jack. Spray the same contact cleaner on an RCA plug, and insert it and twisted back and forth.
- Inspect and tension any shunts on the jack to ensure it’s making contact.
- Repeat for all remaining jacks.
Switches
Switches are pretty simple. You mostly want to ensure they are tight and clean. Toggle switches have different issues than slide switches. Here is my switch checklist and the process I follow depending on which switch is which:
- ☑️ Check positioning of power/standby switches
- ☑️ Tighten nuts or screws to chassis
- ☑️ Clean and lubricate contacts
- ☑️ Inspect solder joints
- Inspect positioning toggle switches to make sure they don’t protrude past the cabinet when possible. This prevents them from being damaged or damaging the chassis if the amp falls over.
- Tighten screws or nuts that connect the switch to the chassis and install locking hardware if necessary.
- Clean and lubricate the switch contacts.
- Inspect the solder joints and reflow solder if necessary.
Tube Sockets
Tube sockets take a beating. In many amps, they are oriented above the tubes they are holding, exposing them to a lot of heat. Over time, this can cause them to become brittle and even chard with carbon. Brittle tube sockets are easy to chip when blindly swapping out tubes in the back of your amp. Here is my tube socket checklist, and the method I use to sock it to ’em:
- ☑️ Pull tubes and inspect sockets
- ☑️ Clean tube sockets surfaces
- ☑️ Tension tube sockets
- ☑️ Clean tube sockets
- ☑️ Clean tube pins
- ☑️ Check movement of tube/socket
- With the chassis oriented so the tubes are facing up, pull the tube from the last tube socket (I like to work backwards from rectifier/output tubes to preamp), and inspect the sockets for corrosion and stretched out contacts.
- Clean the surface of the socket with alcohol.
- Tension any contacts with a tiny flathead screwdriver that look like they might not snugly hold a tube pin. Do not over tension!
- Spray the tiniest amount of non-lubricating contact cleaner into each hole in the socket. Spray a liberal amount of contact cleaner on a toothpick and scrub each contact.
- Spray a liberal amount of contact cleaner on the pins of the tube, and scrub with a clean toothbrush. Reapply contact cleaner to the tube pins and work them in and out of the socket.
- Test the tube and socket for movement and make customer recommendations accordingly. If the socket has a bear trap tube retainer, ensure that it has enough tension to grasp the tube base. It should not touch the glass of the tube!
- Repeat for all remaining tube sockets.
Chassis
Inside the chassis is where attention to detail really pays off. To perform any reasonable inspection on a circuit, you must have magnifiers and plenty of light. You simply cannot spot anything but the most obvious potential problems without them. Behold, my checklist and process for keeping your chassis classy:
- ☑️ Vacuum chassis
- ☑️ Clean chassis
- ☑️ Tighten transformer bolts
- ☑️ Check fuse values
- ☑️ Check mains wiring
- ☑️ Inspect solder joints
- ☑️ Inspect B+ and heater wire condition and connections
- ☑️ Check electrolytic capacitors for leaks
- ☑️ Test resistors
- ☑️ Test ground connections
- Vacuum the entire chassis using a small, stiff-bristled brush to dislodge any debris.
- Clean any corrosion or film off the chassis with alcohol, paying close attention to the area around the input and speaker jacks. This is where liquid spills most commonly enter the chassis.
- Tighten all of the transformer bolts and ensure lock washers, keps nuts or lock nuts are used. Make note of any ground connections made to these bolts. These should be relocated with customer approval.
- Check all fuse values and replace any that don’t match the rated value on the amp. Do not return any replaced fuses with the amp. You don’t want the owner reusing them.
- Inspect mains wiring to see if it is up to code, and make recommendations for customer approval.
- Inspect every solder joint for cracks or dry joints. Tug on wires. Reflow solder where necessary.
- Inspect wires and make notes of any burns and exposed conductors to be replaced with customer approval.
- Check electrolytic capacitors for visible leaks, and make note for customer approval.
- Test resistors and make note of any that are out of spec.
- Inspect all ground connections and reflow or tighten where necessary.
Cabinet
I thoroughly clean every item that comes through my shop. 90% of repairing is cleaning, so why not give every cabinet a head start? Here is my cabinet checklist and process:
- ☑️ Vacuum cabinet
- ☑️ Clean cabinet
- ☑️ Tighten baffle screws/nuts
- ☑️ Tighten handle screws
- ☑️ Tighten speaker nuts
- ☑️ Inspect speaker solder joints
- ☑️ Clean reverb tank bag
- ☑️ Clean reverb tank contacts
- Remove back panels, reverb tank and foot switch from the cabinet, then vacuum thoroughly using a small, stiff-bristled brush to dislodge any debris. Use latex or equivalent gloves when dealing with rodent droppings.
- Clean cabinet exterior using diluted windex and a toothbrush.
- Tighten baffle screws/nuts.
- Tighten handle screws.
- Hand-tighten speaker nuts.
- Inspect speaker solder joints, and reflow if needed, using a paper towel to protect the speaker cone from solder splashes or drips.
- Remove the reverb tank from the bag and clean the bag using diluted windex and a toothbrush.
- Clean the contacts for the reverb tank using the same method in the jacks section above.
That seems like a lot of stuff. I suppose it is, but the more you do it, the faster it goes. I also get a speed boost by addressing one part at a time rather than batching things together. It’s also a super efficient way to find issues while mitigating future potential issues at the same time, which is the whole point! Depending on the repair, this service is often included in your bench fee.
If you are located in the greater Sacramento CA or Bay Areas, and you have an amp, pedal or even a guitar or bass whose electronics are in need of some love, I have lots of it to give. Reach out!